What is the High pressure for a filter press?
Introduction to Filter Press Maximum Pressure
In the world of industrial dewatering, the filter press stands as a pivotal piece of equipment tailored for the efficient removal of solids from liquids. Designed to handle a wide array of slurries, from mining waste to dairy products, the filter press operates on the principle of applying pressure to capture solid particles between filter plates while allowing the liquid to pass through. However, one of the most crucial aspects governing its efficiency and effectiveness is the maximum pressure it can withstand. Understanding this parameter is vital for optimizing the performance of the filter press and ensuring its longevity and safety.
Key Factors Determining Maximum Pressure
● Hydraulic System Capabilities
The hydraulic system in a filter press is the backbone of its pressure capabilities. It is responsible for both closing the filter plates and maintaining the necessary pressure during the filtration process. The power and efficiency of the hydraulic cylinders directly influence the maximum pressure the filter press can achieve. high pressure filter presses require robust hydraulic systems capable of exerting and maintaining pressures ranging from 100 psi to 225 psi, and in specialized applications, even higher.
● Design of Filter Plates and Frames
The design and material composition of the filter plates and frames also play significant roles in determining the maximum pressure. Plates must be robust enough to withstand high pressures without deforming or breaking. Common materials include cast iron, stainless steel, and polypropylene, each offering different balances of strength and corrosion resistance. The frame, typically made from high-strength steel, must support the plates and withstand the cumulative force exerted by the hydraulic system.
Impact of Slurry Composition on Pressure
● Types of Slurries: Hydrophilic vs. Hydrophobic
The composition of the slurry being processed significantly impacts the required pressure. Hydrophilic materials, which have an affinity for water, can be challenging to dewater, often necessitating higher pressures to achieve the desired dryness of the filter cake. In contrast, hydrophobic materials repel water and generally dewater more easily, requiring less pressure. Understanding the nature of the slurry is essential for calibrating the filter press to its optimal settings.
● Particle Size Distribution and Its Effects
The size and shape of the particles within the slurry also affect the filtration pressure. Slurries with larger, rounded particles are more straightforward to dewater as they do not pack as tightly together, allowing water to pass through more easily. On the other hand, fine, flat particles, such as those found in clay-based slurries, can create dense cakes that require higher pressures to process effectively. Adjusting the filter press to accommodate these characteristics ensures the efficient operation of the equipment.
Hydraulic System: Core of Pressure Management
● Role of Hydraulic Cylinders
Hydraulic cylinders are the heart of the pressure system in a filter press. These cylinders exert force to close the plates and maintain the necessary pressure during the filtration cycle. The strength and precision of these cylinders determine the maximum pressure the system can handle, directly impacting the efficiency of the dewatering process. High pressure filter presses are equipped with advanced hydraulic systems designed to handle the rigors of industrial applications.
● Pressure Regulation Mechanisms
Effective pressure regulation is critical for maintaining the integrity of the filter press and ensuring optimal performance. Modern high pressure filter presses often incorporate sophisticated control systems that monitor and adjust the hydraulic pressure in real-time. These systems help prevent over-pressurization, which can lead to equipment damage or failure, and ensure the process operates within safe and efficient parameters.
Material Strength and Design Considerations
● Durability of Filter Plate Materials
The materials used in the construction of filter plates must be chosen for their ability to withstand high pressures and corrosive environments. Common materials include:
- Cast Iron : Known for its strength and durability, suitable for high-pressure applications.
- Stainless Steel : Offers excellent resistance to corrosion and is suitable for a wide range of chemical environments.
- Polypropylene : Lightweight and resistant to a variety of chemicals, making it ideal for less demanding applications.
Each material presents different balances of strength, weight, and chemical resistance, impacting the overall performance and longevity of the filter press.
● Structural Integrity of the Filter Press Frame
The frame of the filter press must support the combined force of the hydraulic system and the plates under pressure. Typically constructed from high-strength steel, the frame must be designed to handle the maximum pressure the system can generate without deforming or failing. A well-designed frame ensures the filter press operates safely and efficiently, even under high-pressure conditions.
Standard Pressure Ranges in Modern Filter Presses
● Typical Operating Pressures: 100-225 psi
Most modern filter presses are designed to operate within a standard pressure range of 100 psi to 225 psi. This range is sufficient for the majority of industrial applications, providing the necessary force to achieve efficient dewatering without compromising the integrity of the equipment. The specific operating pressure within this range is determined by the characteristics of the slurry and the desired dryness of the filter cake.
● Special Applications Requiring Higher Pressures
Certain specialized applications may require pressures above the standard range. For instance, processing highly viscous or difficult-to-dewater slurries may necessitate pressures exceeding 225 psi. High pressure filter presses designed for these applications are equipped with reinforced plates and frames, and more powerful hydraulic systems to handle the increased demands.
Optimization of Pressure for Efficient Filtration
● Balancing High Pressure with Filtration Efficiency
While higher pressures can enhance dewatering efficiency, there is a balance to be struck. Excessive pressure can lead to increased wear and tear on the filter cloths and plates, reducing the equipment's lifespan. It is essential to optimize the pressure to achieve the desired filtration efficiency while minimizing maintenance and replacement costs. This balance is often achieved through trial and error, guided by experience and expertise.
● Pressure Adjustments for Different Slurry Types
Different slurry types require different pressure settings for optimal dewatering. By adjusting the pressure based on the slurry's composition and particle size distribution, operators can optimize the filtration cycle. High pressure filter presses that allow for easy adjustment and fine-tuning of pressure settings are invaluable for handling a variety of slurries efficiently.
Safety Concerns and Pressure Limits
● Risks of Exceeding Maximum Pressure
Exceeding the maximum pressure of a filter press can lead to catastrophic failures, including the rupture of filter plates, damage to the hydraulic system, and potential injury to operators. It is crucial to adhere to the manufacturer's recommended pressure limits and ensure that all safety mechanisms are in place and functioning correctly. Regular maintenance and inspections help prevent accidental over-pressurization.
● Safety Mechanisms in Place to Prevent Accidents
Modern high pressure filter presses are equipped with various safety mechanisms to prevent accidents. These include pressure relief valves, automatic shutoff systems, and real-time monitoring of hydraulic pressures. These safety features are designed to detect and respond to over-pressurization, ensuring the filter press operates within safe limits at all times.
Technological Advances in Pressure Handling
● Innovations in Hydraulic Systems
Advances in hydraulic technology have significantly enhanced the pressure handling capabilities of modern filter presses. Innovations such as electronically controlled hydraulic systems and variable pressure settings allow for more precise control and adjustment of operating pressures. These improvements result in better dewatering efficiency and extended equipment lifespan.
● Enhanced Materials for Higher Pressure Capabilities
The development of new materials with superior strength and chemical resistance has also contributed to the ability of filter presses to handle higher pressures. Advanced composites and alloys are increasingly being used in the construction of filter plates and frames, offering enhanced durability and performance. These materials enable high pressure filter presses to operate at pressures previously considered unattainable.
Conclusion: Achieving Ideal Pressure Balance
The maximum pressure a filter press can handle is a critical factor in its overall performance and efficiency. By understanding the key factors that determine this pressure, such as the capabilities of the hydraulic system, the design and materials of the filter plates and frame, and the composition of the slurry, operators can optimize the dewatering process. Safety concerns must always be a priority, with appropriate mechanisms in place to prevent accidents. Technological advances in hydraulic systems and materials continue to push the boundaries of what is possible, enabling high pressure filter presses to achieve new levels of performance.
● Introducing HZfilter
HZfilter is a leading manufacturer and supplier of high pressure filter presses. With a commitment to innovation and quality, HZfilter provides advanced dewatering solutions tailored to meet the needs of various industries. Their state-of-the-art facilities and expert team ensure that each filter press is built to the highest standards of performance and reliability. For more information, visit [HZfilter]
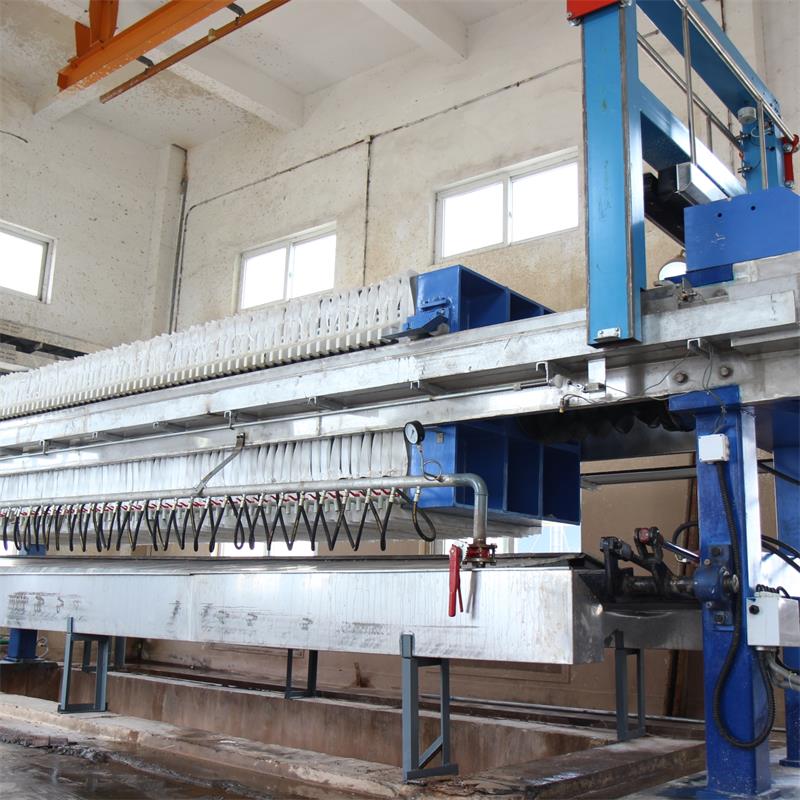
评论
发表评论