How do you increase filter press efficiency?
Introduction to Filter Press Efficiency
In industrial processes across various sectors, the efficiency of filter presses is paramount. Whether it's in mining, chemical processing, or wastewater treatment, a highly efficient filter press can lead to significant cost savings, improved productivity, and enhanced product quality. Filter press efficiency can be affected by numerous factors and understanding these is crucial for optimal operation. This article will delve into the key strategies for increasing filter press efficiency, from optimizing feed pump pressure to selecting the right filter media and maintaining proper cake formation.
Optimizing Feed Pump Pressure
● Impact of Feed Pressure on Efficiency
Feed pump pressure plays a critical role in the performance of a filter press. The pressure must be high enough to drive the slurry through the filter media but not so high that it causes excessive wear or damage. Incorrect pressure settings can lead to inefficient filtration, increased cycle times, and higher operational costs.
● Best Practices for Pressure Settings
To optimize feed pump pressure, it is important to monitor and adjust the pressure settings based on the specific requirements of the filtration process. Many overhead filter press manufacturers provide guidelines on ideal pressure settings. Regular calibration and maintenance of the feed pump are necessary to ensure consistency. Utilizing pressure sensors and automated control systems can help maintain the ideal pressure range, ensuring efficient filtration cycles.
Selecting the Right Filter Media
● Types of Filter Media and Their Applications
The choice of filter media is a critical factor in determining filter press efficiency. The filter media must balance the need for permeability, strength, and resistance to chemical attack. Common types of filter media include woven fabrics, nonwoven fabrics, paper, and synthetic membranes. Each type has its applications, with woven fabrics often used for their durability and synthetic membranes for their precise filtration capabilities.
● Criteria for Selecting Filter Media
Selecting the right filter media involves considering the nature of the slurry, the desired filtration rate, and the required level of purity. It's essential to work closely with your overhead filter press supplier to determine the most appropriate filter media for your specific application. Consideration should also be given to the cost of the media and its lifespan under operating conditions.
Maintaining Proper Cake Formation
● Factors Affecting Cake Formation
The formation of a uniform and consistent filter cake is vital for efficient filtration. Factors such as the properties of the slurry, the feed rate, and the filter media type influence cake formation. Poor cake formation can lead to longer filtration cycles and lower filtrate clarity.
● Techniques to Improve Cake Consistency
To improve cake consistency, it's important to manage the concentration and particle size distribution of the slurry. Pre-treatment of the slurry, such as through flocculation or coagulation, can enhance cake formation. Adjusting the filtration cycle parameters and ensuring the even distribution of the slurry across the filter press plates also contribute to better cake quality.
Ensuring Adequate System Maintenance
● Regular Maintenance Schedules
Regular maintenance is key to the longevity and efficiency of a filter press system. A well-maintained system is less likely to experience downtime or require costly repairs. Establishing a comprehensive maintenance schedule that includes routine inspections, cleaning, and part replacements is essential.
● Key Components to Monitor and Service
Key components such as the filter plates, cloths, hydraulic systems, and feed pumps should be regularly inspected for wear and tear. Ensuring these components operate effectively helps maintain consistent filtration performance. Engaging with an overhead filter press manufacturer for professional servicing can also be beneficial.
Automating the Filtration Process
● Benefits of Automation
Automation in filtration processes can significantly enhance efficiency by reducing human error, improving consistency, and enabling real-time adjustments. Automated systems can monitor various parameters such as feed pressure, filtration cycle time, and cake thickness, making necessary adjustments to optimize performance.
● Technologies for Automating Filter Presses
Modern filter presses can be equipped with advanced control systems, including programmable logic controllers (PLCs) and human-machine interfaces (HMIs). These technologies allow for precise control over the filtration process, from feed pressure management to cake discharge. Automation can be particularly advantageous for overhead filter press factories looking to scale up their operations while maintaining high efficiency.
Managing Slurry Characteristics
● Influence of Slurry Composition on Filtration
The characteristics of the slurry being filtered, including its particle size, viscosity, and chemical composition, heavily influence filtration efficiency. Slurries with a high concentration of fine particles can clog filter media, while those with high viscosity can slow down filtration rates.
● Methods to Modify Slurry Properties
Adjusting slurry properties to optimize filtration involves several techniques. Pre-treatment processes such as flocculation, coagulation, and pH adjustment can help improve slurry characteristics. Collaborating with an overhead filter press supplier to identify the right additives and treatment methods is crucial.
Utilizing Filter Aids and Additives
● Types of Filter Aids and Their Functions
Filter aids such as diatomaceous earth, perlite, and cellulose can enhance filtration by creating a porous, permeable layer on the filter media. This layer helps to prevent clogging and improves the clarity of the filtrate. Additives can also help in binding fine particles, making them easier to filter.
● Guidelines for Effective Use of Additives
The use of filter aids and additives should be carefully managed to avoid excessive costs and maintain filtration effectiveness. It's important to determine the optimal dosage and mixing procedures. Working with an experienced overhead filter press supplier can provide valuable insights into the best practices for using filter aids.
Improving Cake Discharge and Cleaning
● Efficient Cake Discharge Techniques
Efficient cake discharge is crucial to maintaining short cycle times and high productivity. Techniques such as vibration, pneumatic discharge, or mechanical scrapers can be used to facilitate cake removal. Ensuring the filter press is designed for easy cake discharge, as is often the case with models from an established overhead filter press manufacturer, can also be beneficial.
● Cleaning Protocols to Reduce Downtime
Regular cleaning of the filter press and its components helps prevent buildup and fouling. Implementing automated cleaning systems can reduce downtime and labor costs. Establishing standardized cleaning protocols ensures consistency and maintains the efficiency of the filter press over the long term.
Monitoring and Analyzing Performance Metrics
● Key Performance Indicators for Filter Presses
To effectively increase filter press efficiency, it is essential to monitor key performance indicators (KPIs) such as cycle time, filtrate clarity, cake thickness, and equipment downtime. These metrics provide valuable insights into the performance of the filtration process and help identify areas for improvement.
● Tools and Technologies for Performance Analysis
Advanced monitoring tools such as sensors, data loggers, and software analytics can provide real-time data on the filtration process. Utilizing these technologies enables proactive management and timely adjustments. Collaborating with an overhead filter press supplier can help in selecting and implementing the right analytical tools.
HZfilter Company Introduction
HZfilter independently develops and produces complete sets of filtering equipment, including filter presses suitable for various industries, large-scale energy-saving and efficient filter presses with circulating plates, various mixers, thickeners, horizontal energy-saving piston wear-free feed pumps, and pressure vessels of different forms. It undertakes customized business both domestically and internationally. Widely used in environmental protection, mining, chemical industry, new energy, new materials, food, and biomedicine, HZfilter has focused on continuously satisfying users for over 30 years. Understanding customer needs and providing the best solutions is their commitment.
By following the strategies outlined in this article, industries can significantly improve their filter press efficiency. Whether through optimizing feed pump pressure, selecting the right filter media, or utilizing automation and advanced monitoring tools, each step contributes to a more efficient and productive filtration process. Working with reputable overhead filter press suppliers and manufacturers such as HZfilter can provide the necessary expertise and equipment to achieve these improvements.
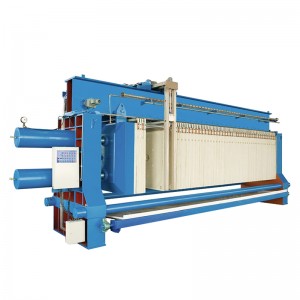
评论
发表评论